-
題名
学ぶ、学び舎
-
所在地
東京都小金井市貫井北町4-1-1
-
用途
集会所兼木工所
-
構造
RC造
-
階数
地上1階
-
敷地面積
297471.22㎡
-
建築面積
251.28㎡
-
延床面積
295.90㎡
-
竣工
2023年8月
-
建築設計
VUILD(担当/秋吉浩気 中澤宏行 篠原岳 伊勢坊健太 高野和哉(元所員))
-
生産設計アドバイス
ヴィック(担当/渡辺 健児 石原隆裕)
-
構造設計
佐藤淳構造設計事務所(担当/佐藤淳 本田幾久世(元所員) 末廣康介 下田悠太)
-
環境設備
Arup(担当/菅健太郎 大江晴天(元所員) 土井豊希)
-
照明
TILe(担当/岩壁泰良)
-
監理
VUILD(担当/秋吉浩気 中澤宏行 篠原岳 伊勢坊健太)
-
施工
アトリエ海 (担当/佐々木君吉 田中岳(鉄建建設より出向))
-
木材加工
VUILD ( 担当/花田康史 小西陽二 野田慎治)
-
電気
大東電設(担当/片岡雅生)
-
写真
太田拓実
次世代の学びを探求するプロジェクトとして建設された教育インキュベーション施設である。CLTを型枠にした鉄筋コンクリート造を構造とする。CNC加工された葉脈状梁やパネルをコンクリートの型枠として使用し、仕上げを兼ねた「打ち込み型枠」として残す。これを主要構造体として機能させ、建築として使用した前例のない構造物である。曲面の幾何学的なアルゴリズムによりCADモデルを自動生成し、それを補助線として5軸CNC加工のCAMのパスを作成し、自社で木製型枠を切削する、という通常の意匠設計および構造設計の枠を超えたシステムを構築した。建物内にはこの型枠を加工したCNC加工機が設置され、先端製造技術を誰でも体験することができる開放的な施設として活用される予定であり、 必要な空間や場を、利用者が都度拡張していくというオープンエンドな建築となっている。そのため、初期条件として大屋根と機械だけがある状態から始まる。
⚫︎デザインプロセス
設計の課題として、次世代の新しい公教育を実装する場としての役割を持たせつつ、完成形のない、拡張可能な空間としての開放的な空間を作り出すというものがあった。また、学習材となりうる「教材として」のエクストリームでエクスペリメンタルな建築が求められた。そこで5軸CNC加工機による3次元切削を用いた大スパンの空間を作り出すとした。最大240㎜厚のCLTパネルから切り出せることを条件とし、全体形状と切り出しの都合の間でシミュレーションを繰り返し、最適化の試行錯誤が重ねられた。場所によっては単純化を用い、あくまで施工を念頭に置いたデザインプロセスとなっている。
⚫︎ユニット工法+残存型枠
CLT梁は長手断面をサインカーブ状の曲線にし,その振幅の位相を短手方向にずらしていくことで,強いシェルをつくるという方法を探索していった。形状としては、度重なるスタディの末、自然界に見られる葉脈に倣った屋根形状になった。ジグザクに断面を構成することでシェルのデプスをつくり,そのジグザク断面の位相を3層にずらしていくことで強度を持たせた。 これにCLTのパネルを3次元的に自社工場でユニット切削し、現場で梁に接合、パネル同士は短冊金物でつなげた。そこにコンクリートを流し、葉脈上の梁と葉脈間を覆うスラブという構造体へと発展させた。そして木梁のスパン25m、コンクリートスラブの厚さ8cmという薄さを実現している。この建築工法は特開2021-042568として特許申請されており、汎用性の高い工法として通常のシェル工法の6割のコストに収めることができた。
3次元データは構造設計者と共有され、解析にも使うことができるので、いわゆるヒューマンエラーを避けることができる。このデータを、設計、意匠チェック、構造解析、ファブリケーションのための部材作成のすべてにおいてクロスチェックできるようになっていたことで迅速なプロセスを実現できた。
⚫︎加工データ作成、材料調達から施工までのシステム構築
5軸加工では,傾きと回転が特徴的であり、それを考慮に入れた最適化が要求された。5軸切削を行うためにパスを作る必要があるが、パーツ数は合計360枚のCLTパネルから963パーツの型枠を加工するという複雑なものであった。自社のパラメトリックチームにより自由曲面の幾何学的なアルゴリズムが自動的にCAD化できるように開発された。このパス作成のフローでは,加工後の手加工を減らすことも条件として設計された。またコンクリートで隠れるような箇所では,適切な許容範囲において曲面を粗く加工し,加工コストを抑えた。
コスト削減を目的として効率的にパネルを配置した。使用したCLT板は,1,350×4,000mmを上限に複数種類のものを用意した。CLT板には60~210mmの間に4通りの厚みがあり,どの厚みの板にネスティングされているかを示す色をパネルに割り当てた.これによってどの板から切り出すべきかを簡単に判断できた。このフローを構造チームとも共有することで、構造・施工利便性の両方の観点での最適化のシステムを構築することができたのである。
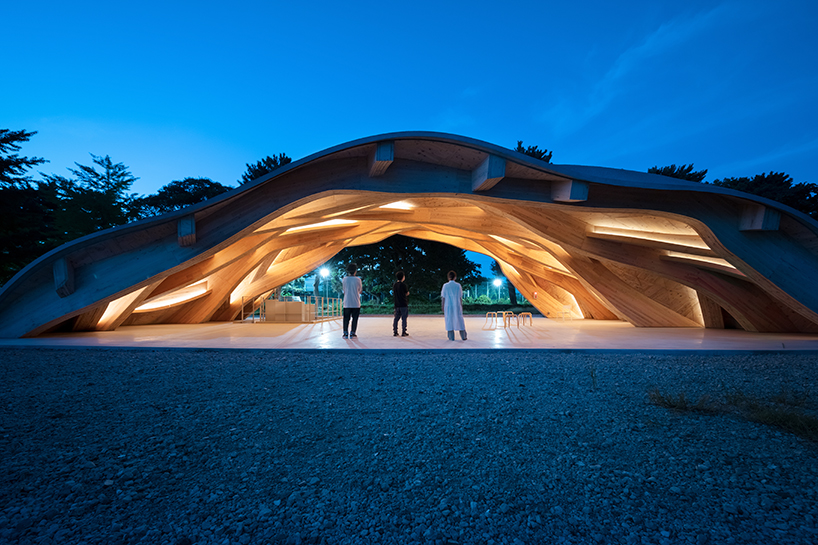
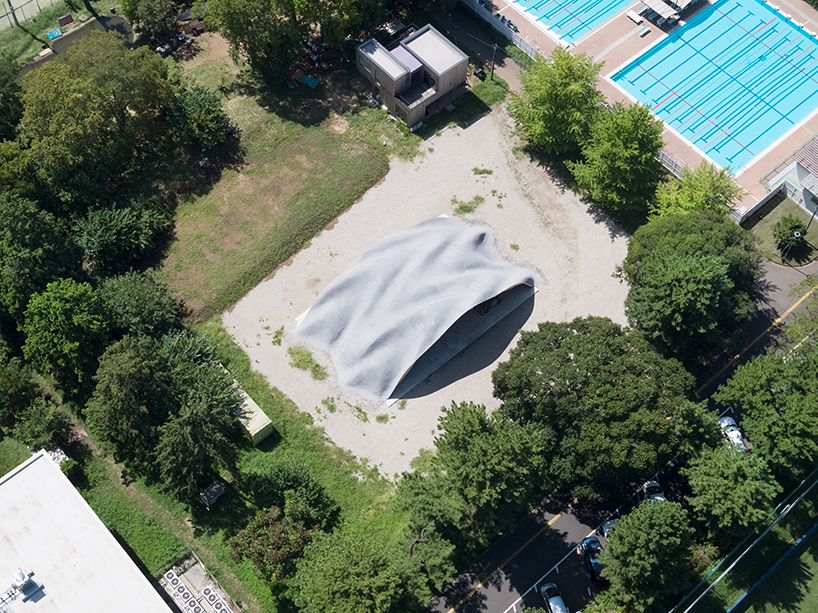