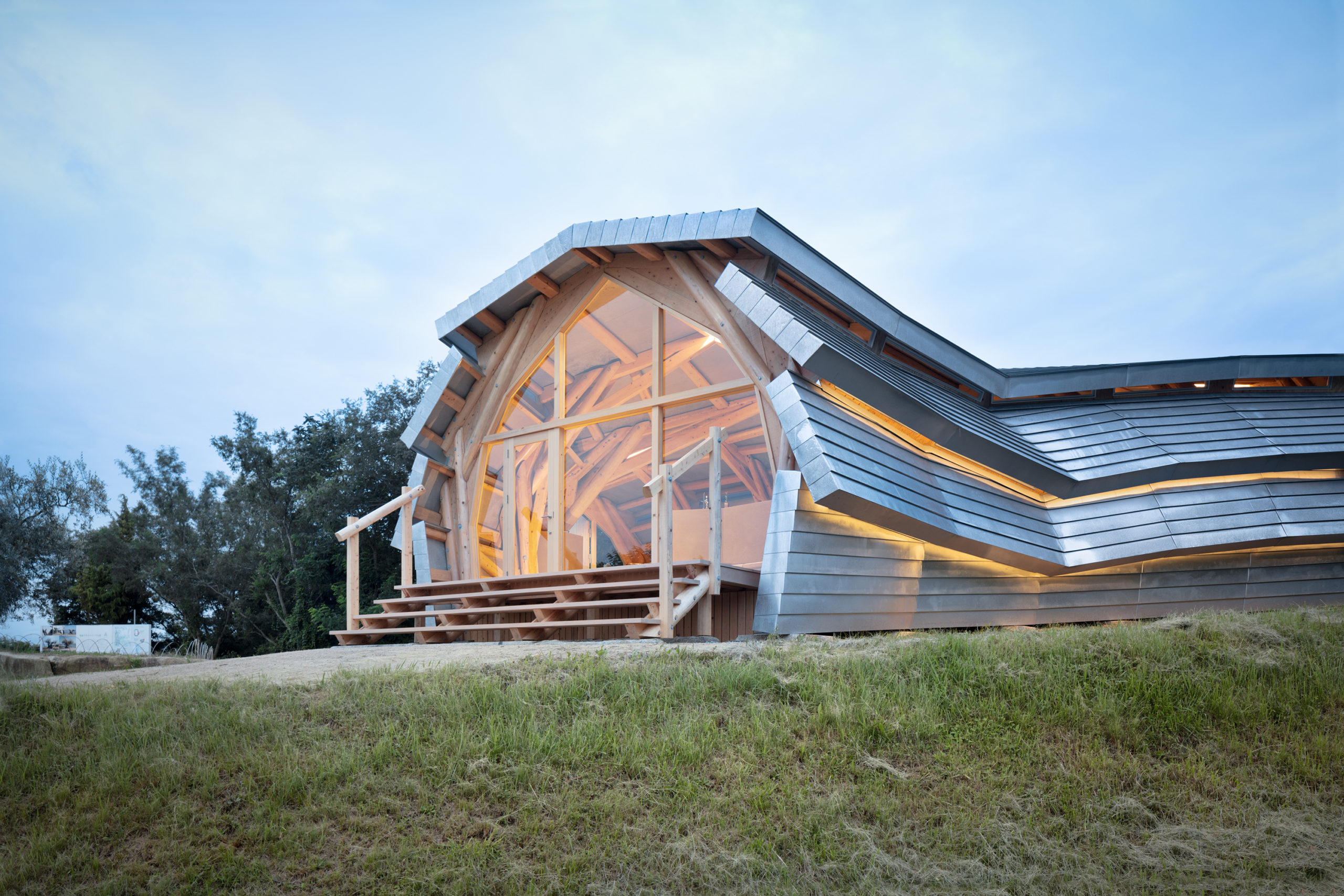
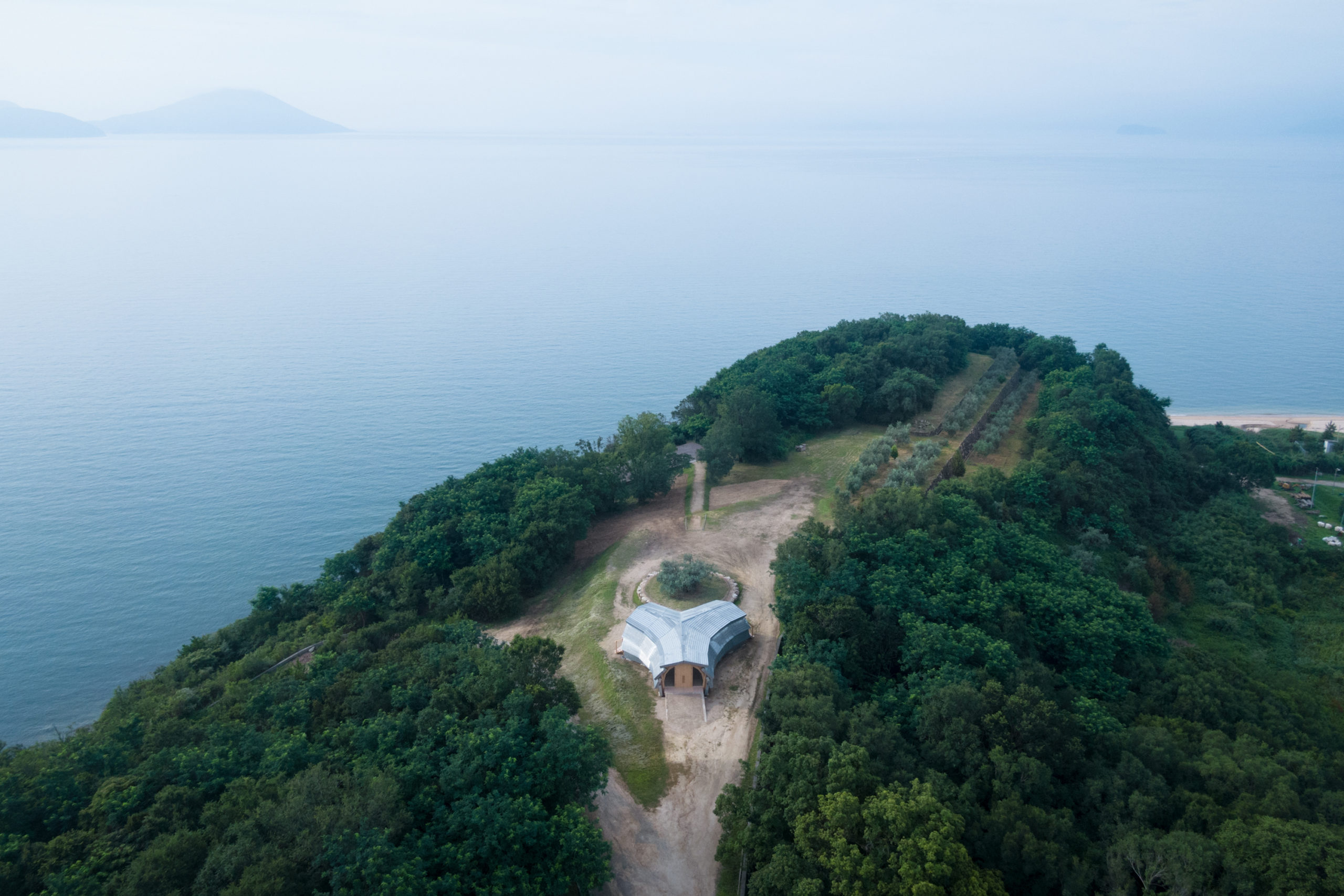
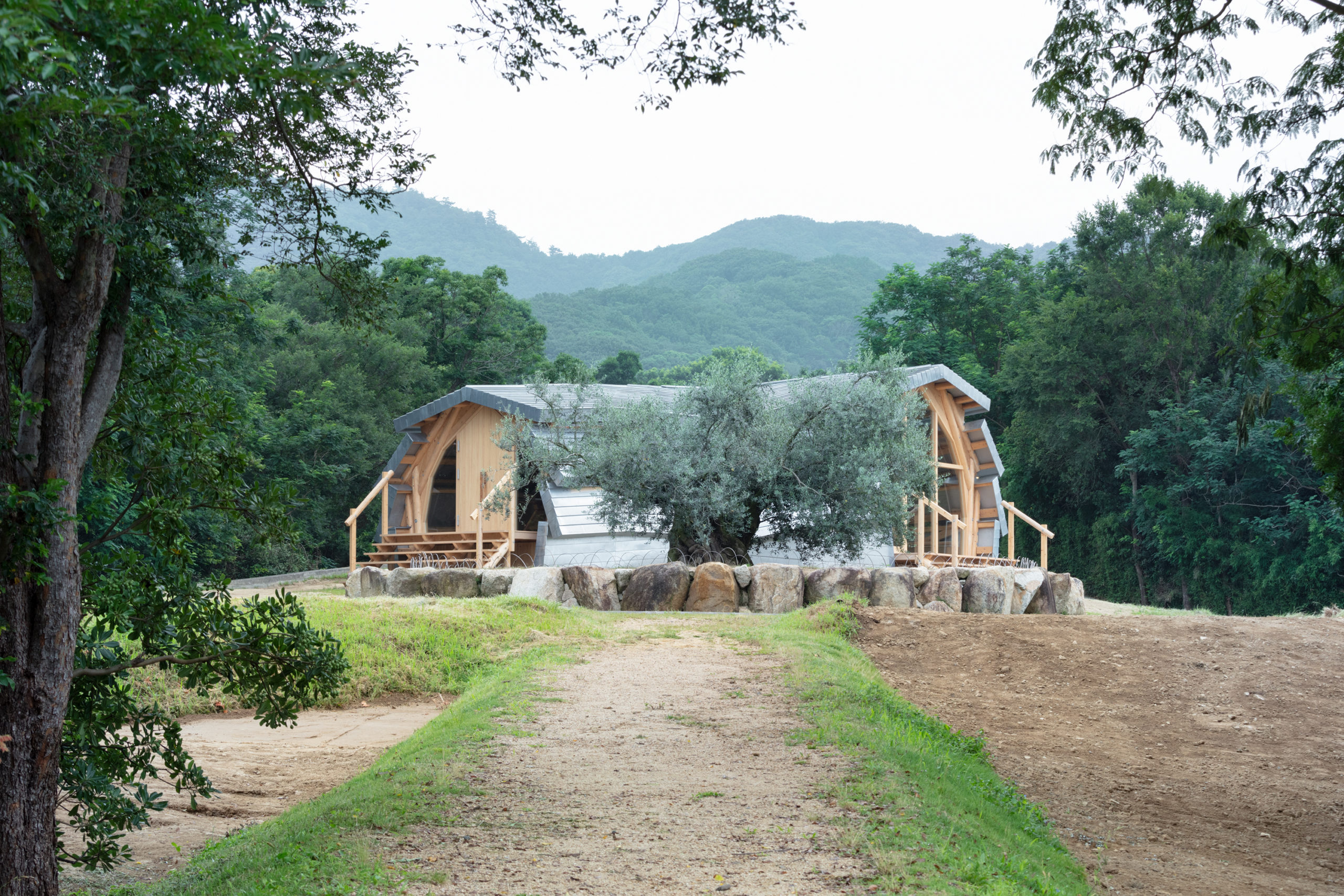
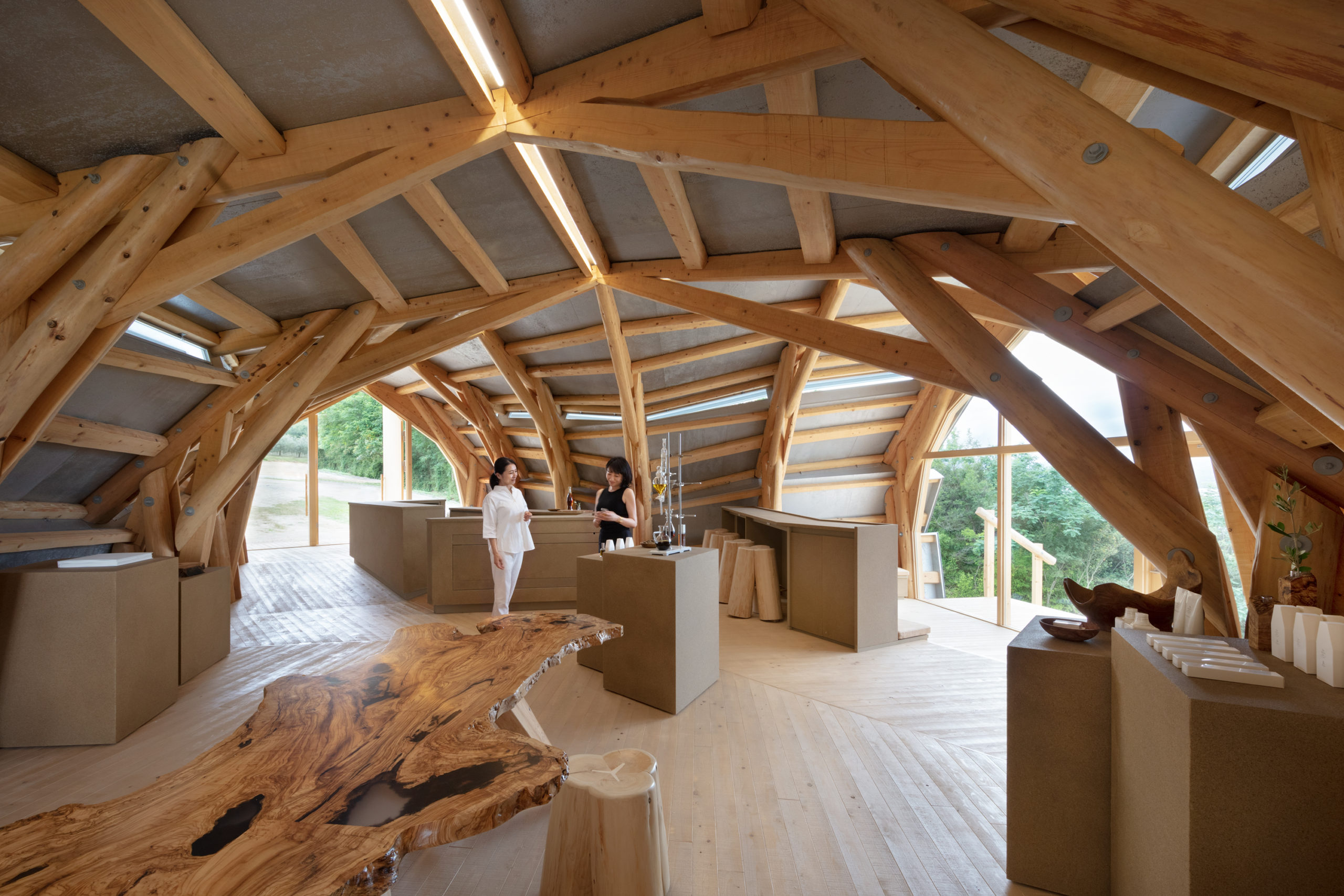
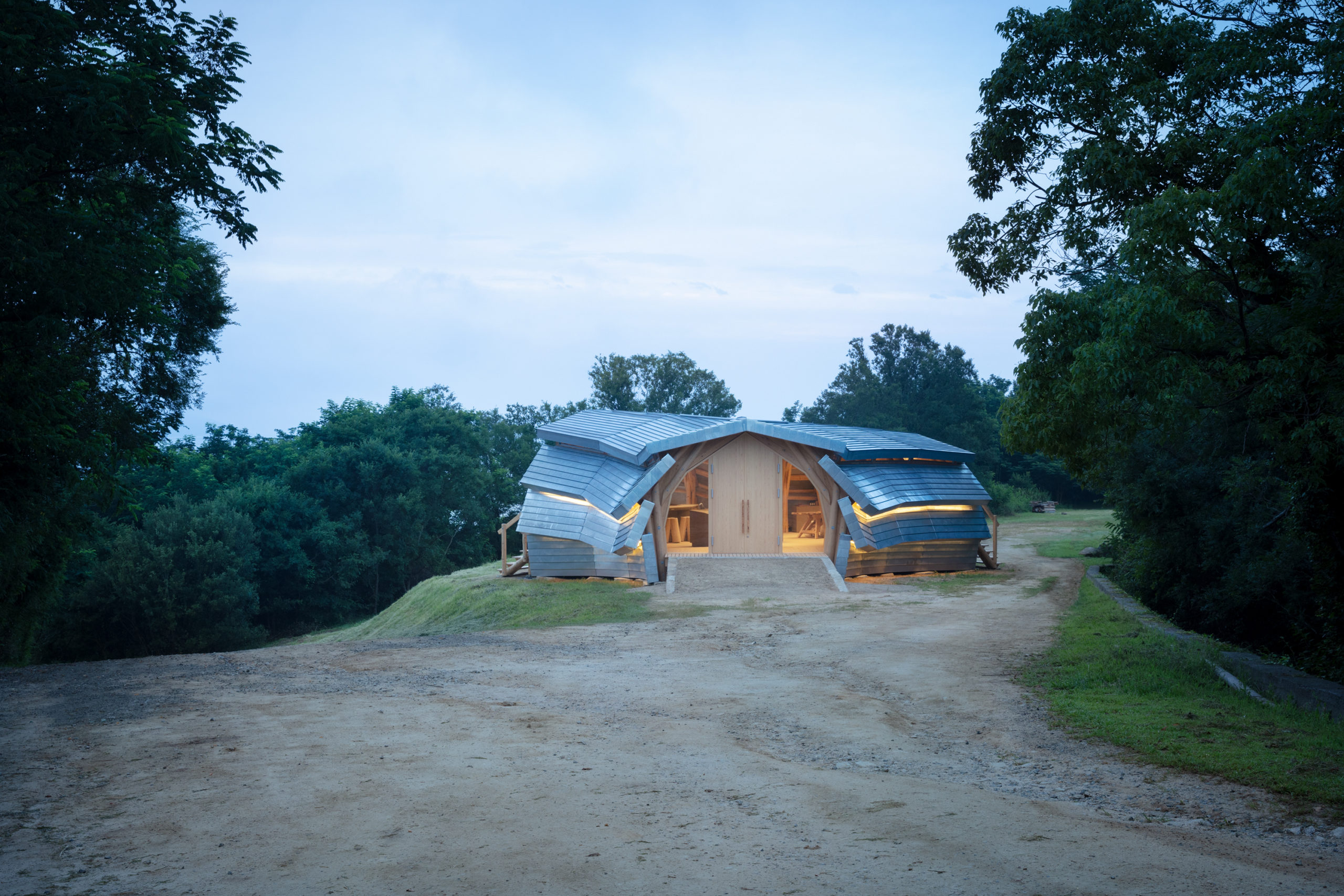
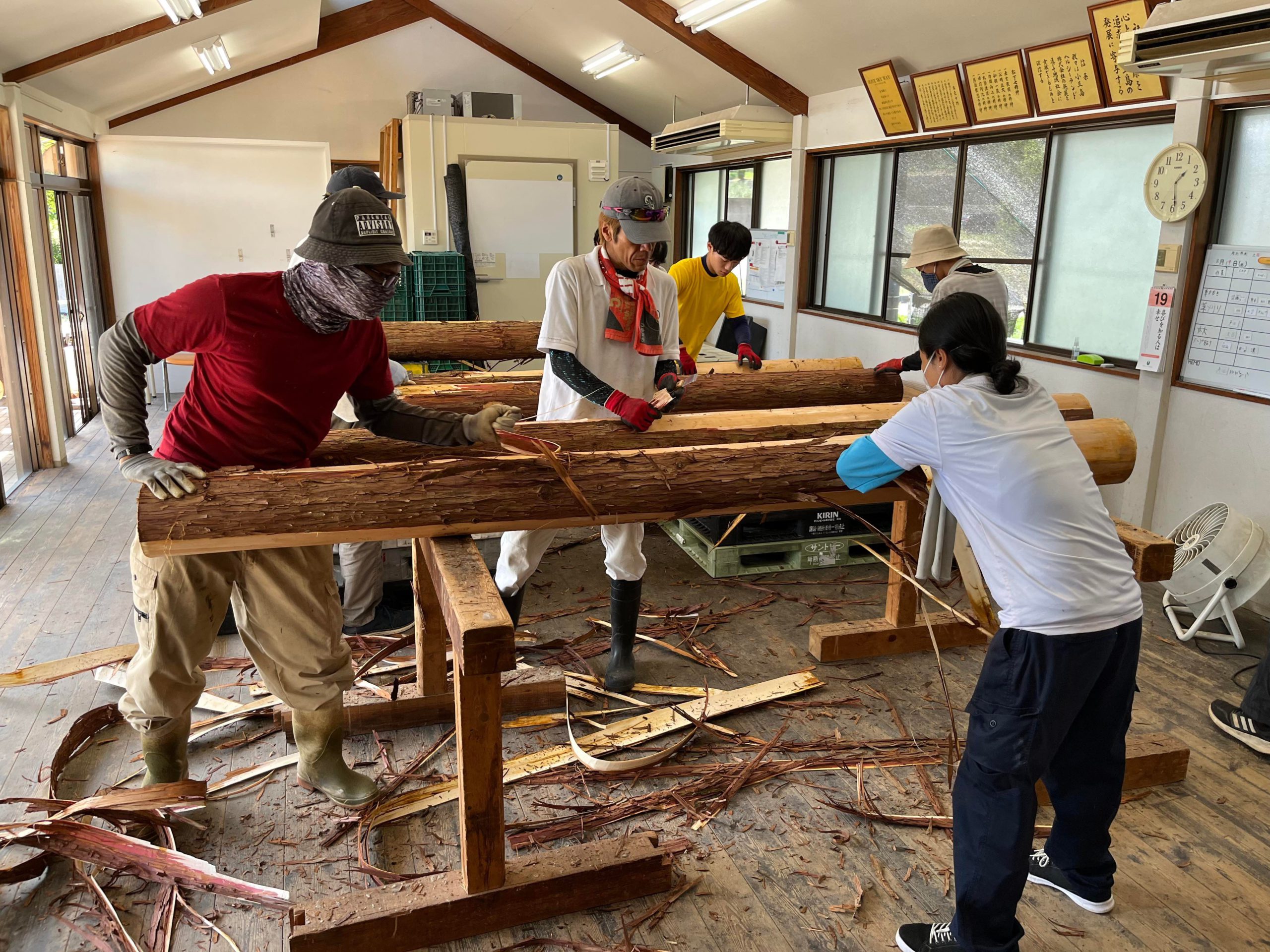
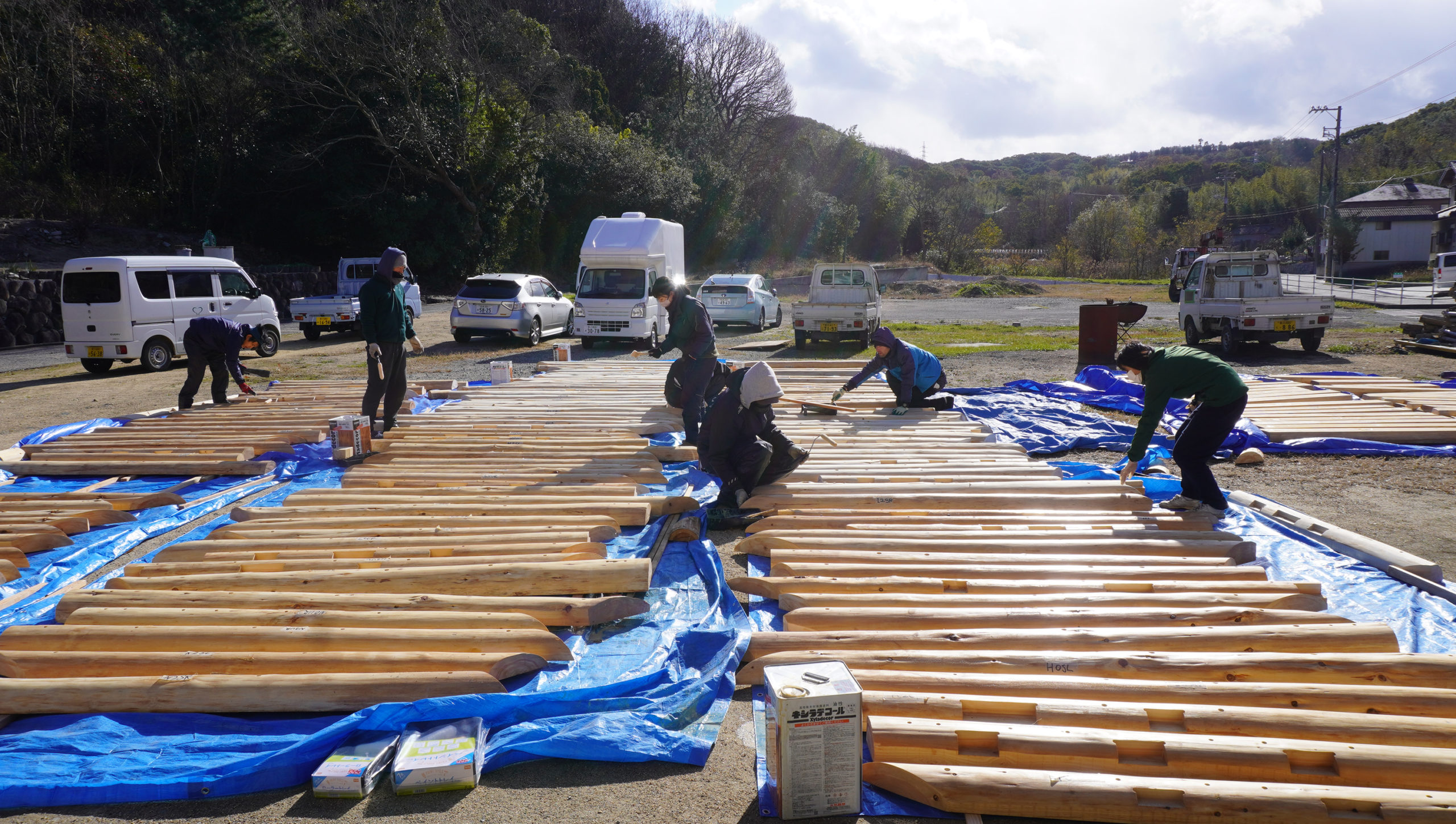
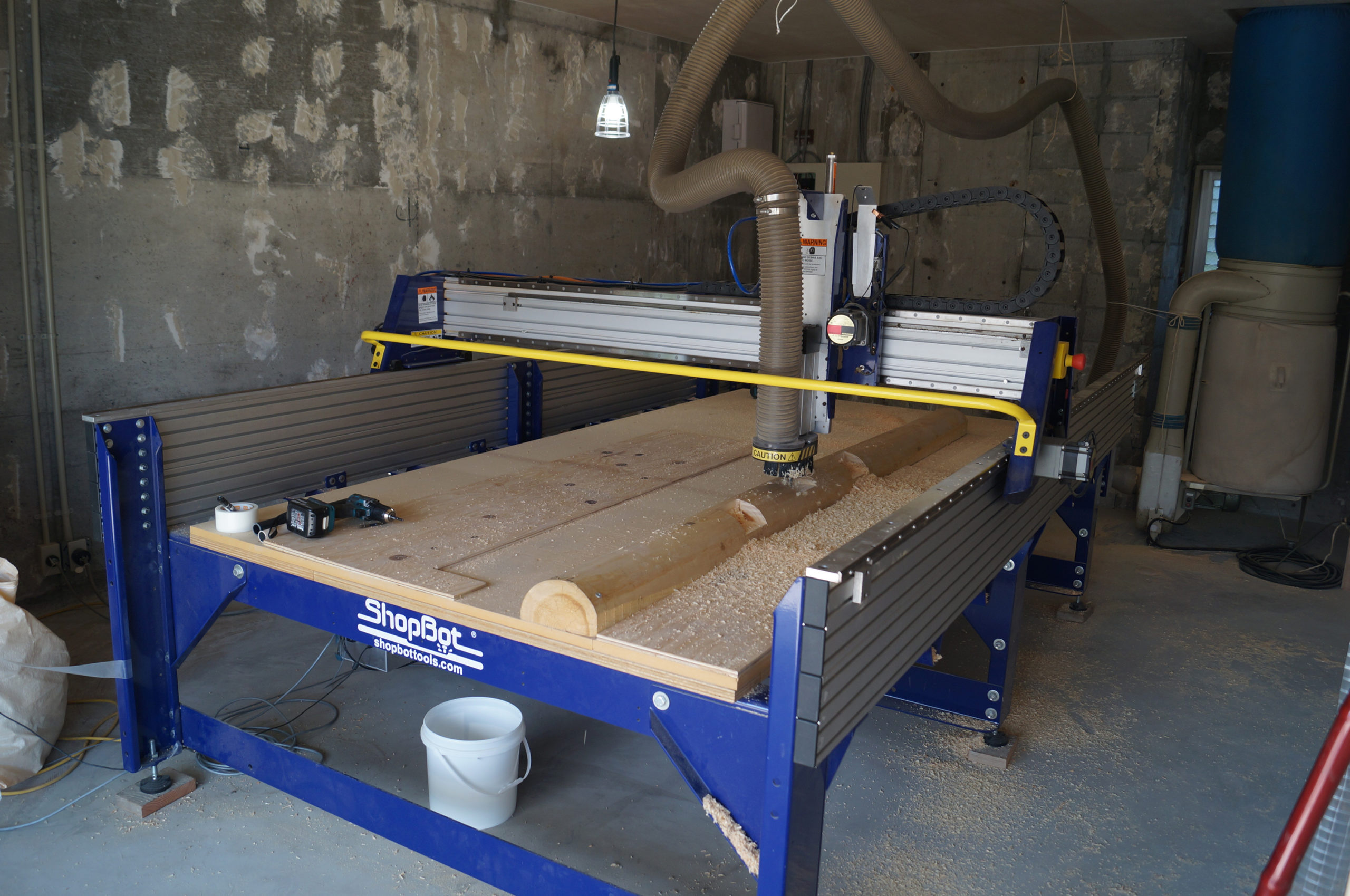
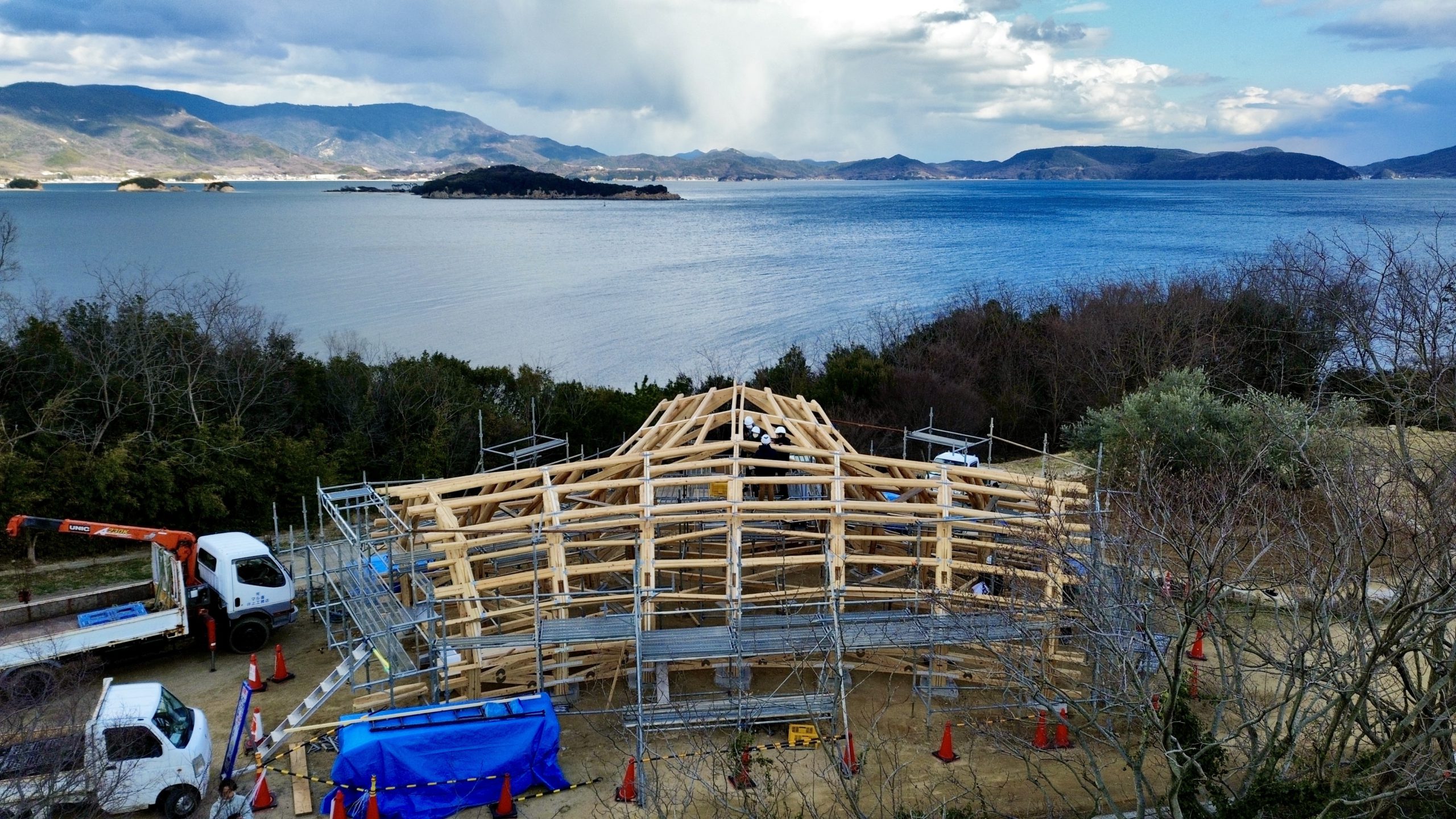
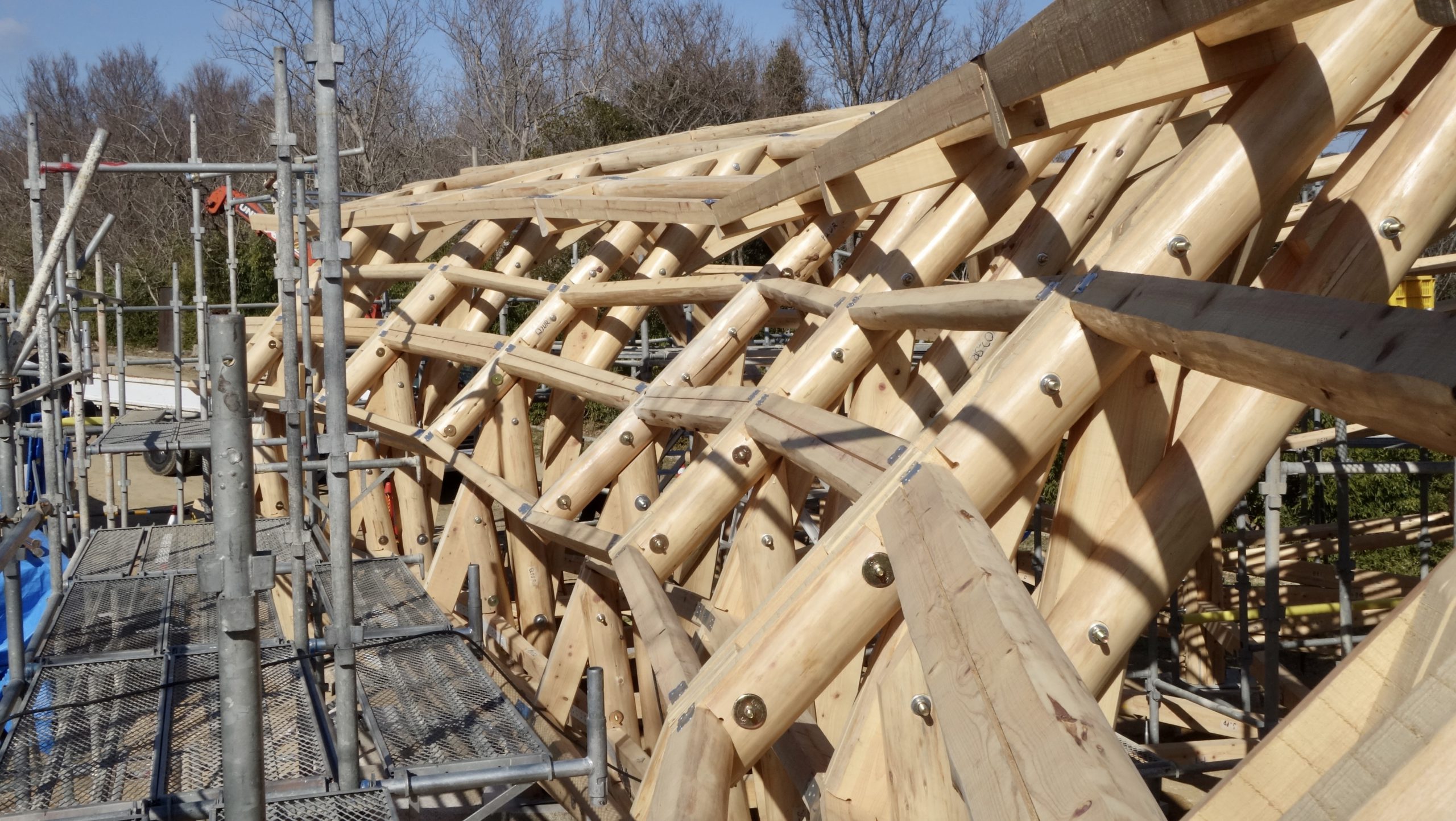
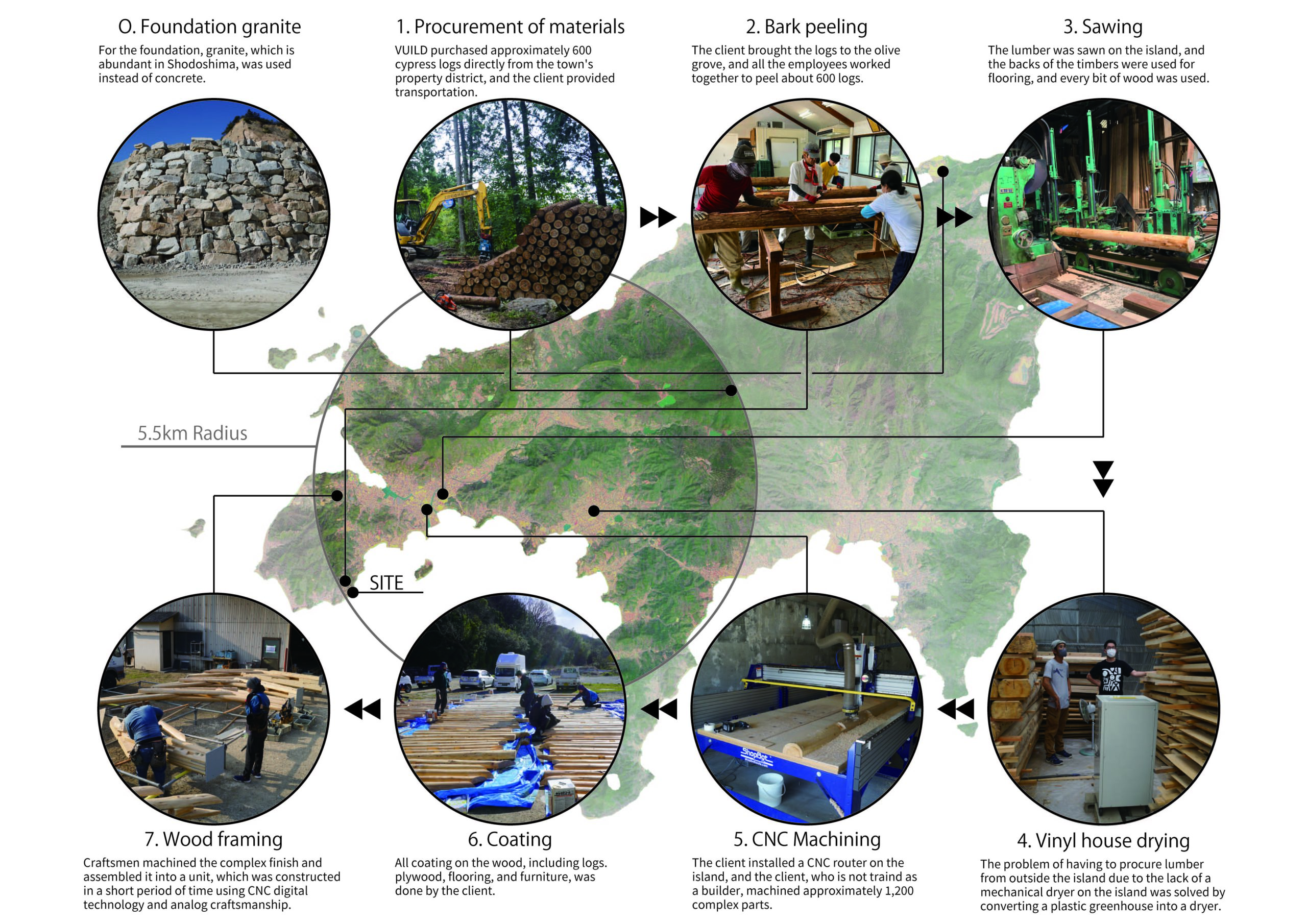
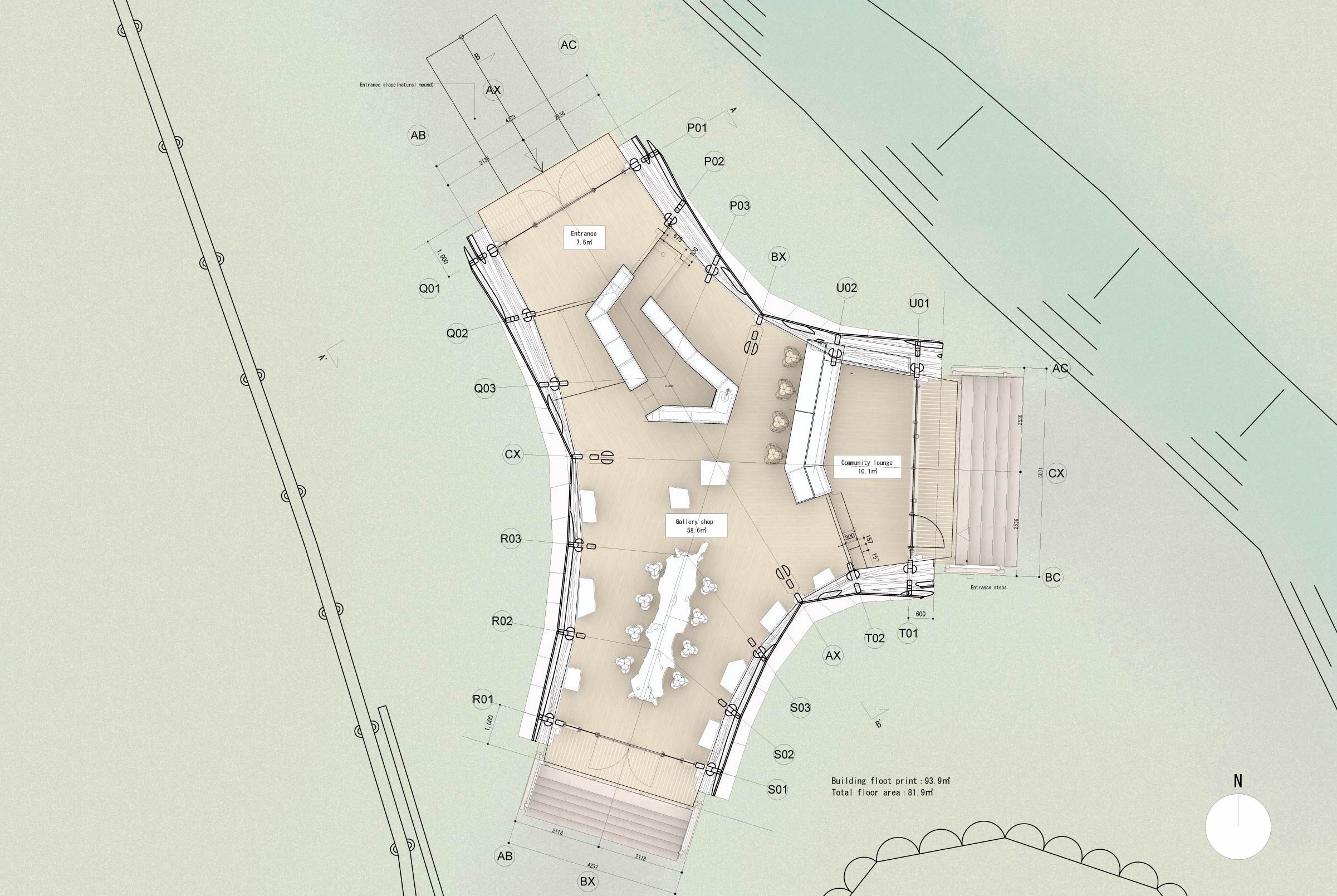
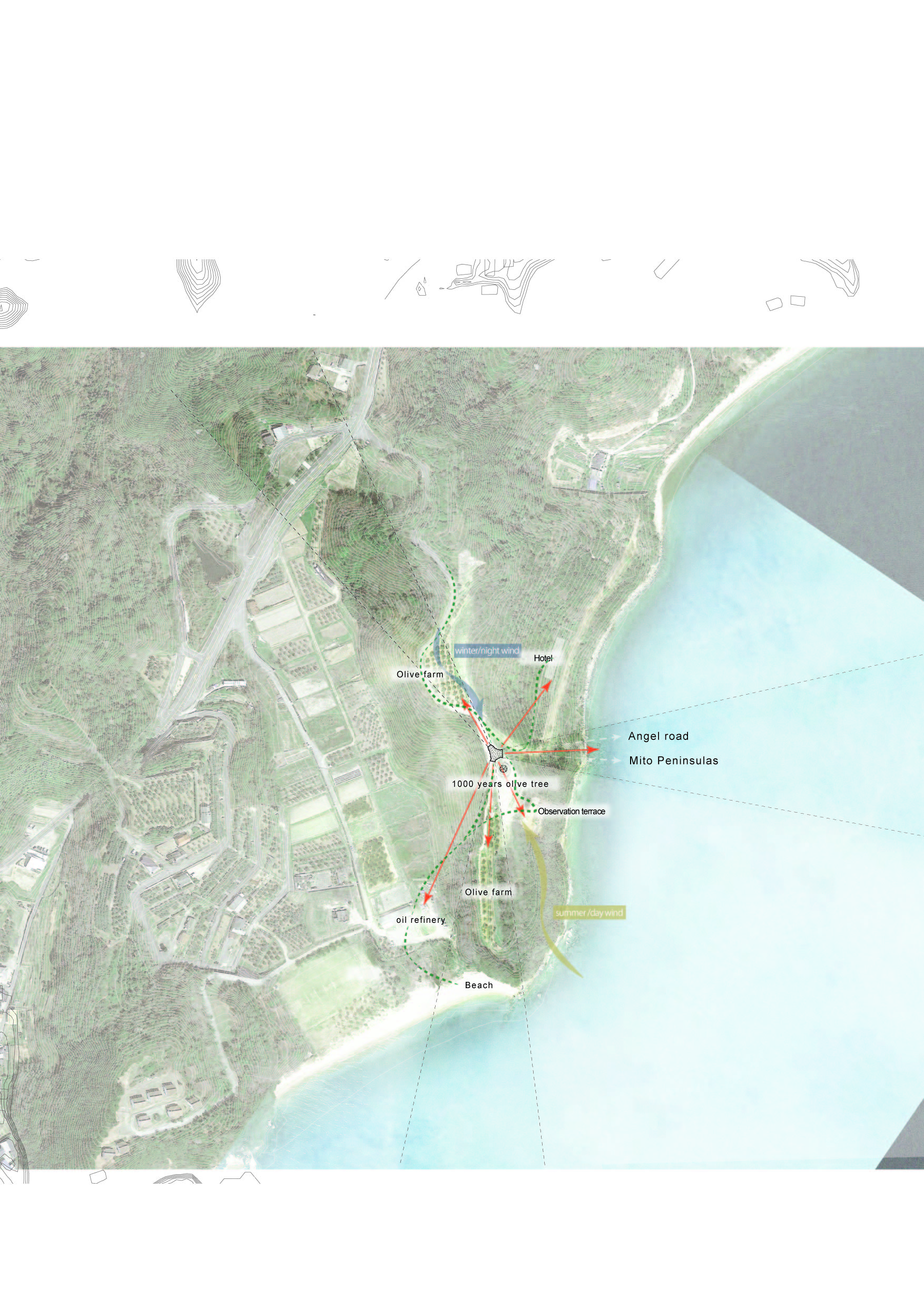
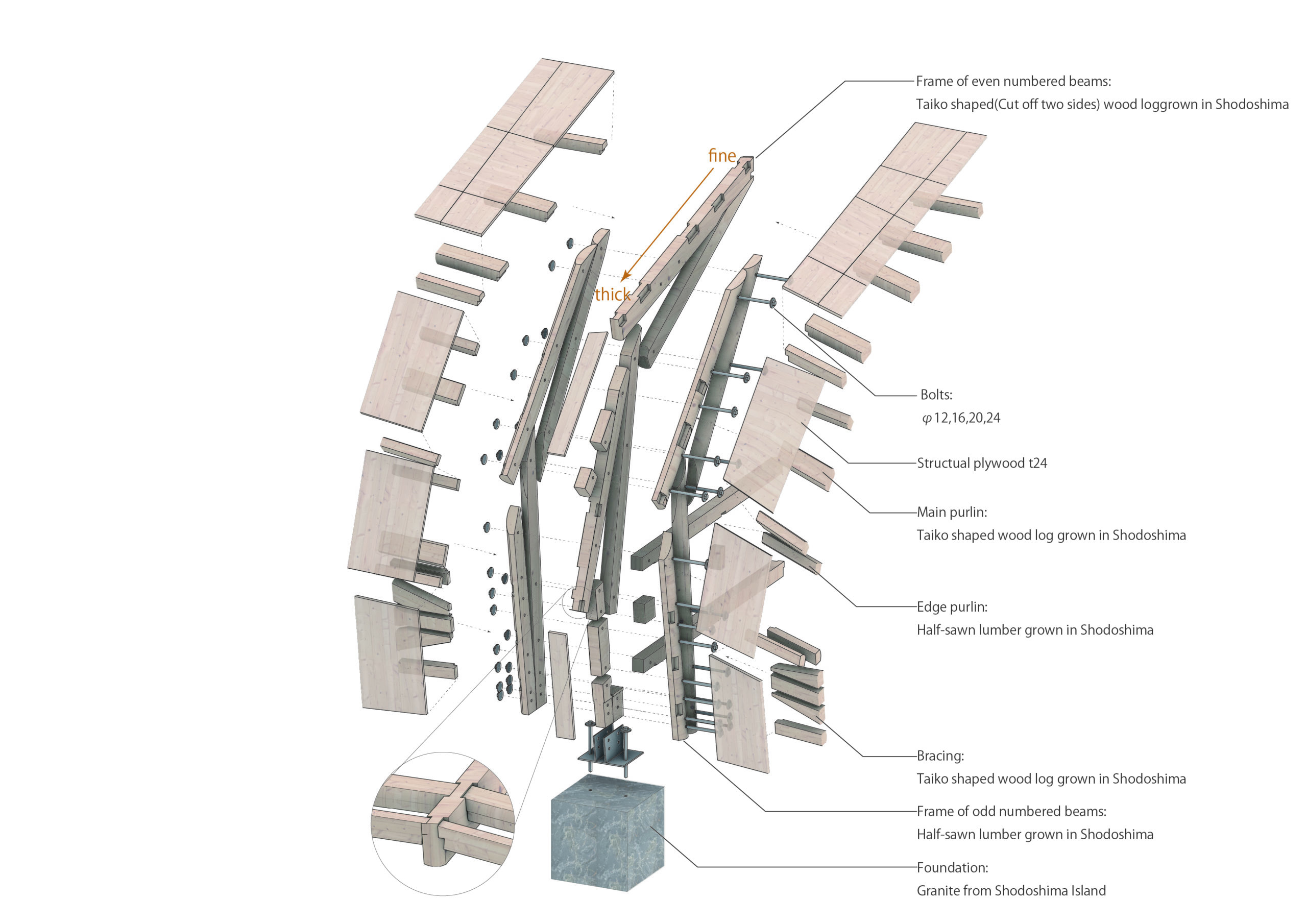
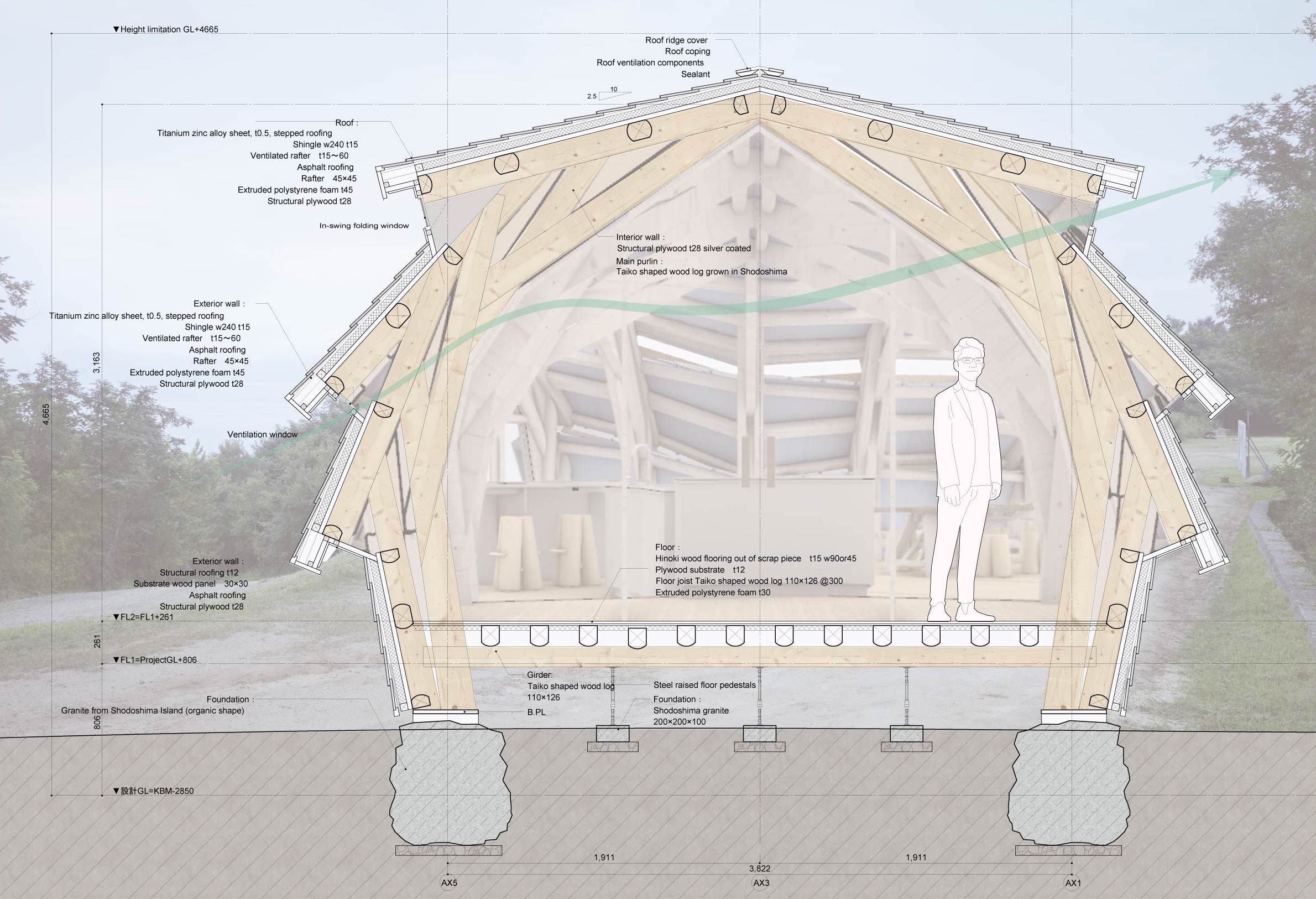
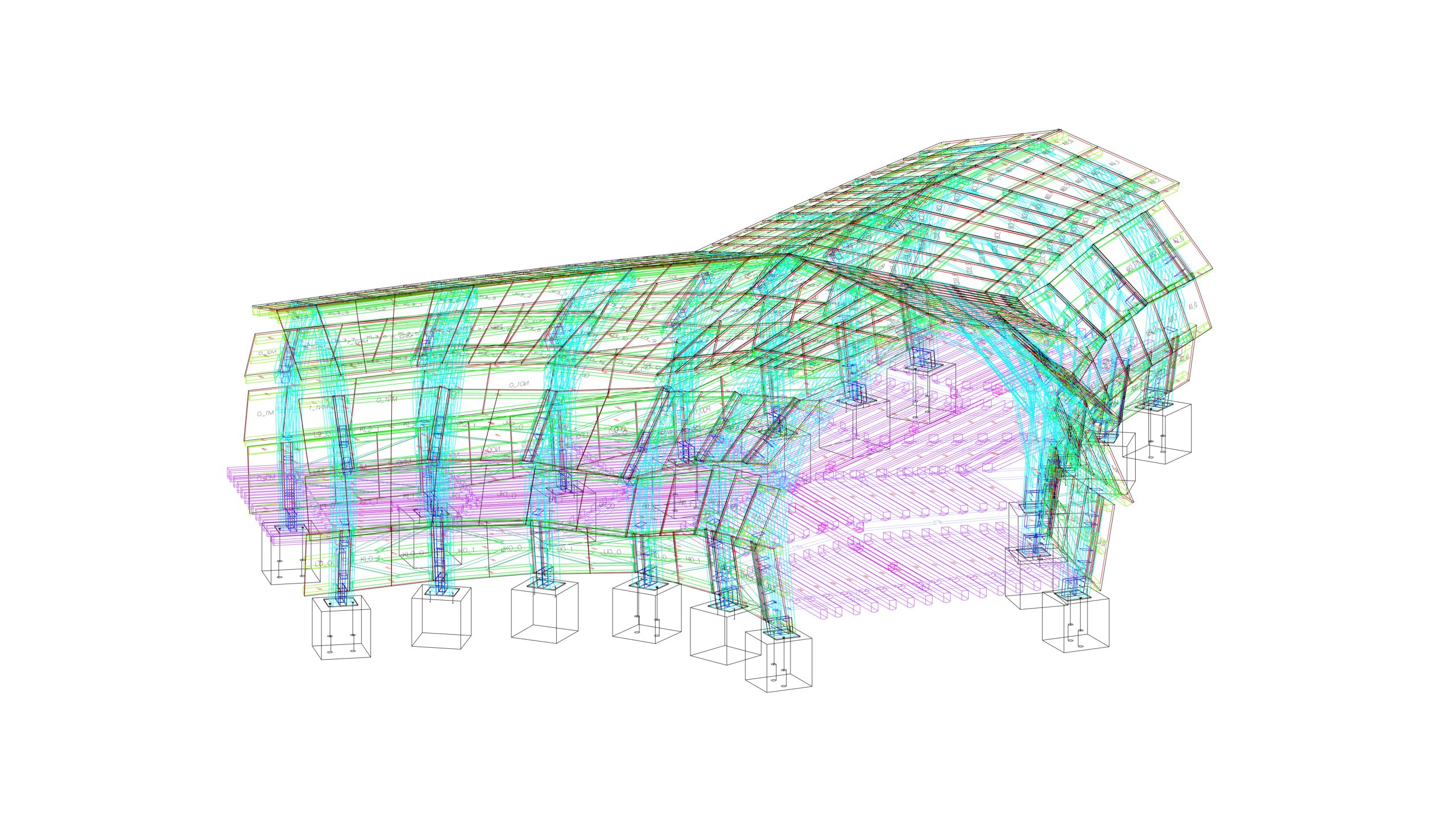

ムービー
-
Design Team
VUILD (Koki Akiyoshi Akito Nakai Hiroyuki Nakazawa)
-
Computational Design
VUILD (Kenta Isebo)
-
Design Adviser
ondesign (Osamu Nishida
-
Structural Design
Graph Studio (Mika Araki Kei Uzioka)
-
Environmental Design
Stusio Nora (Keichiro Taniguchi Masaki Fujimura)
-
Lighting Design
TILe (Taira Iwakabe)
-
Photo(completion photo)
Takumi Ota
1.Introduction
VUILD completes ‘Shodoshima the GATE LOUNGE‘ proposing new relationship between designers and clients overcoming challenges to establish a supply chain on a remote island by only using resources on the island.
2.Design challenge
Shodoshima Island is located in western Japan, 180 km west of Osaka. When designing a wooden structure on this island, lumber was previously transported from main land at great cost due to the lack of drying and processing facilities on the island; VUILD proposed to create their own facilities by converting a plastic greenhouse into a drying machine and installing a small CNC processing machine in order to utilize the existing cypress trees on the island. Believing that this would be beneficial to both the local community and the global environment, the client agreed to a policy of procuring materials and building the facility with their own hands, and this project was completed with their cooperation.
The client traveled the island to find the stone and wood for the foundation, and the carbon footprint from the source was kept to a minimum within a 5.5 km radius. The client himself transported the materials, peeled, milled, and painted the wood under the guidance of the architect and contractor. VUILD took on the difficult challenge of guiding and coordinating design and construction under these conditions.
3. Program
The program is a shop and facility for the client, who is involved in the cultivation, research and development, production, and sales of olives on Shodoshima island. The client had been selling olive products and cosmetics online, but as their business grew, they felt the need to create a place for face-to-face sales and interaction. In addition to experiencing the products and services, visitors can observe the actual cultivation and pressing process, and enjoy the climate and landscapes that nurtured the olives through their five senses during their stay. VUILD designed a place with the function of a gate as a starting point for such experiences and a lounge where the host and visitors, visitors and visitors can interact.
4. Environmental consideration
The site faces the sea, and the building is positioned to wrap around a symbolic 1,000-year-old olive tree. The direction of wind and light was carefully considered in the architectural design. The flow of daylight and wind was simulated by a sustainability engineer, and the building’s three-way spreading form encourages natural ventilation and multi-directional flow to the site. The walls have three layers of slits for lighting and ventilation, and on sunny days, natural lighting of about 500 lx can be expected even in the center of the building. The building shape, which is divided into three sections, also has the effect of catching the wind from the sea, and by drawing the captured wind into the room through the slits, it can be expected to have a natural lighting effect of about 500 lx even in the center of the building on a sunny day.
By drawing the captured wind into the rooms through the slits, a gentle air flow of around 0.3 m/s can be felt at all times, even when the entrance doors are closed.
Instead of a concrete foundation, huge granite stones from the region were used for the foundation, and the 600 cypress logs used for the structural frame were all logged in the region.
5. Use of Technology and Construction Methods
The challenge of this project was not only to design the space for the user and design it environmentally, but also to accurately create the cutting data for the CNC machine to machine the components to assemble the structure and walls. Such intricate fabrication used to be done only by skilled carpenters, but digital fabrication technology has made it possible for anyone to produce accurate woodwork details.
Structurally, the intricately cut members for the end joints were pre-assembled to create a sectional unit of arched logs. Half-sawn logs and drums were alternately combined and bolted together to transfer stresses. The log diameter was set at 150 to 200 mm, which is easy to obtain in Shodoshima island, and the length was set at 2.5 m or less based on CNC machine’s maximum cutting ability. Under these conditions, the form was determined to be close to the axial force system for vertical loads and to reduce thrust.